Jak się robi cement? Szczegółowy przewodnik krok po kroku do idealnej produkcji
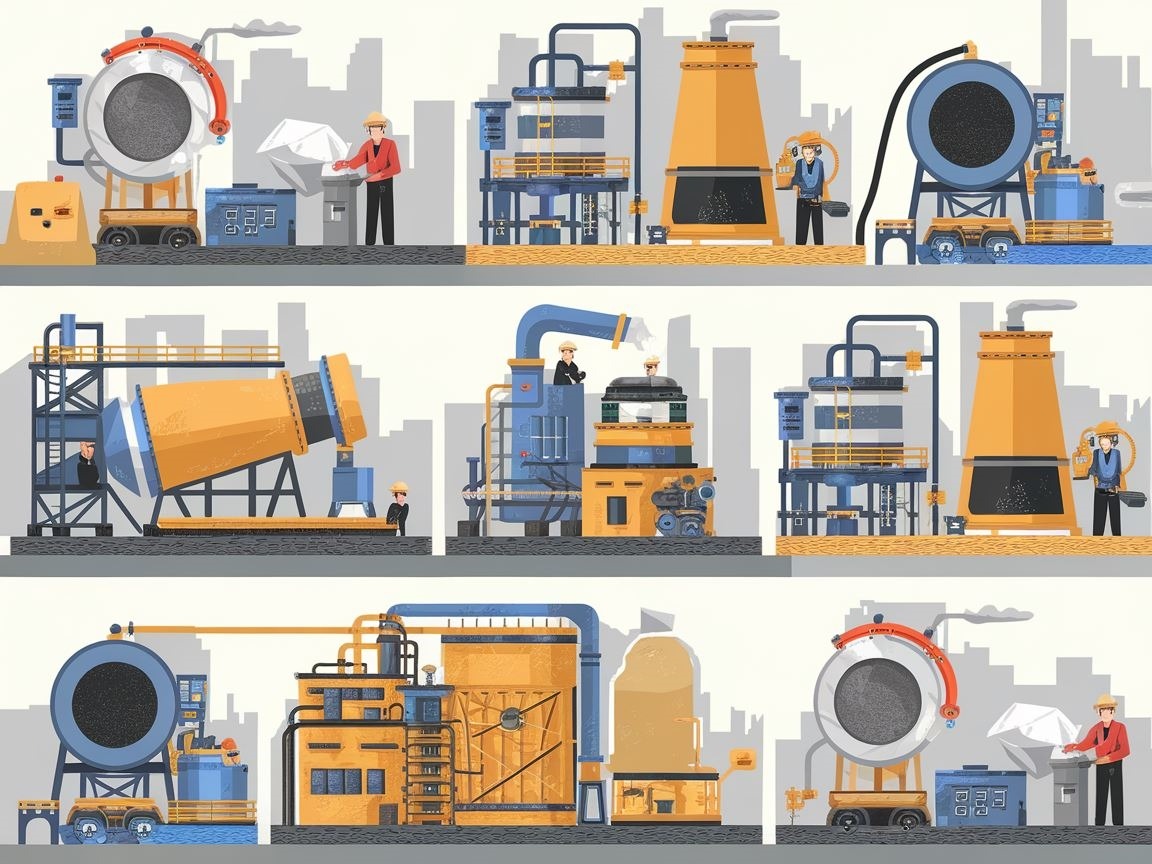
- Cement to podstawowy materiał budowlany znany od starożytności
- Proces produkcji obejmuje kilka kluczowych etapów technologicznych
- Główne surowce to wapień, margiel i minerały ilaste
- Klinkier cementowy wypalany jest w temperaturze do 1450°C
- Dodatek gipsu reguluje czas wiązania gotowego cementu
Produkcja cementu to fascynujący proces technologiczny, który łączy tradycyjne metody z nowoczesnymi technologiami przemysłowymi. Historia tego materiału sięga czasów starożytnych – już Rzymianie wykorzystywali beton, którego składnikiem był cement, do wznoszenia monumentalnych budowli. Według najnowszych badań, podobne materiały mogły być używane jeszcze wcześniej, nawet przy budowie egipskich piramid. Współczesny proces produkcji cementu to precyzyjnie kontrolowany ciąg operacji, które przekształcają naturalne kopaliny w uniwersalny materiał wiążący, bez którego trudno wyobrazić sobie współczesne budownictwo.
Czy zastanawiałeś się kiedyś, skąd bierze się ten szary proszek, który stanowi podstawę większości konstrukcji budowlanych? W niniejszym artykule przybliżymy proces wytwarzania cementu krok po kroku, od wydobycia surowców po finalny produkt. Zrozumienie tego procesu pozwala lepiej poznać właściwości cementu i jego zachowanie w różnych warunkach, co ma kluczowe znaczenie dla trwałości wznoszonych konstrukcji i optymalnego wykorzystania tego materiału w praktyce budowlanej.
Od surowca do półproduktu – początkowe etapy produkcji
Pierwszym etapem produkcji cementu jest wydobycie i przygotowanie surowców naturalnych, które stanowią bazę dla tego materiału. Główne składniki to kopaliny naturalne: wapień, wapień marglisty, margiel oraz minerały ilaste, zawierające niezbędne pierwiastki takie jak wapń, krzem, glin, żelazo i tlen. Surowce te pozyskuje się w kopalniach odkrywkowych, zazwyczaj zlokalizowanych w pobliżu cementowni, co minimalizuje koszty transportu i zmniejsza ślad węglowy produkcji. Na tym etapie kluczowe znaczenie ma odpowiednia selekcja i mieszanie surowców, ponieważ ich skład chemiczny bezpośrednio wpływa na jakość końcowego produktu.
Po wydobyciu, surowce poddawane są procesowi kruszenia i wstępnego uśredniania składu. Jest to niezmiernie istotny etap, ponieważ tylko utrzymanie stałego składu surowca gwarantuje optymalną jakość klinkieru cementowego, który jest sercem całego procesu produkcji. Następnie rozdrobniony materiał trafia do młyna kulowego lub rolowo-misowego, gdzie odbywa się jego przemiał. Na tym etapie skład surowca może być korygowany poprzez dodawanie różnych dodatków, aby uzyskać mieszankę o pożądanych właściwościach. Precyzyjne przygotowanie i homogenizacja surowców to fundament wysokiej jakości cementu, dlatego nowoczesne cementownie wykorzystują zaawansowane systemy kontroli jakości, aby monitorować skład mieszanki na każdym etapie produkcji.
Wypalanie klinkieru i finalny produkt
Po zmieleniu i dokładnym wymieszaniu, surowiec kierowany jest do pieców obrotowych, gdzie rozpoczyna się najważniejszy etap produkcji cementu – wypalanie klinkieru. W tych gigantycznych, obracających się piecach, surowiec poddawany jest działaniu temperatury dochodzącej do 1450°C. W tych ekstremalnych warunkach zachodzi szereg złożonych reakcji fizykochemicznych, w wyniku których pierwotne minerały przekształcają się w związki charakterystyczne dla klinkieru cementowego: krzemiany, gliniany i glinianoželaziany wapnia. Te nowo powstałe związki chemiczne nadają klinkierowi jego wyjątkowe właściwości wiążące, które aktywują się po kontakcie z wodą.
Ostatnim etapem produkcji cementu jest przemiał klinkieru wraz z dodatkami modyfikującymi właściwości końcowego produktu. Najważniejszym dodatkiem jest gips (siarczan wapnia), który pełni rolę regulatora czasu wiązania cementu. Bez tego dodatku cement wiązałby zbyt szybko, co uniemożliwiałoby jego praktyczne zastosowanie. W zależności od pożądanych właściwości końcowego produktu, do przemiału mogą być również dodawane inne składniki, takie jak popioły lotne, żużel wielkopiecowy czy wapień. Dodatki te pozwalają uzyskać różne rodzaje cementów o specyficznych właściwościach, dostosowanych do konkretnych zastosowań budowlanych.
- Jakie surowce są potrzebne do produkcji cementu? Do produkcji cementu potrzebne są głównie kopaliny naturalne, takie jak wapień, wapień marglisty, margiel oraz minerały ilaste, które zawierają niezbędne pierwiastki: wapń, krzem, glin, żelazo i tlen.
- Jaka jest temperatura wypalania klinkieru cementowego? Klinkier cementowy wypalany jest w temperaturze dochodzącej do 1450°C, co umożliwia zajście niezbędnych reakcji fizykochemicznych.
- Dlaczego do cementu dodaje się gips? Gips (siarczan wapnia) dodawany jest do cementu jako regulator czasu wiązania. Bez gipsu cement wiązałby zbyt szybko, co uniemożliwiałoby jego praktyczne zastosowanie.
- Jakie są główne rodzaje cementu dostępne na rynku? Główne rodzaje cementu to: cement portlandzki czysty (CEM I), cement portlandzki z dodatkami (CEM II) oraz cement hutniczy (CEM III), które różnią się składem i właściwościami.
Etap produkcji | Kluczowe procesy | Znaczenie dla jakości cementu |
---|---|---|
Wydobycie surowców | Eksploatacja kopalin, kruszenie, uśrednianie | Zapewnienie stabilnego składu chemicznego |
Przemiał surowca | Mielenie, homogenizacja, korygowanie składu | Przygotowanie mieszanki o odpowiednim składzie |
Wypalanie klinkieru | Ogrzewanie do 1450°C, reakcje fizykochemiczne | Utworzenie związków o właściwościach wiążących |
Przemiał cementu | Mielenie klinkieru z gipsem i dodatkami | Nadanie cementowi końcowych właściwości użytkowych |
ŹRÓDŁO:
- [1]https://nieruchomosci.infor.pl/budowa/310027,Krok-po-kroku-Jak-powstaje-cement.html[1]
- [2]https://budownictwob2b.pl/przegrody/baza-wiedzy/fundamenty/51873-cement-podstawowy-produkt-budowlany[2]
- [3]https://e-sciany.pl/cement-rodzaje-i-zastosowanie/ar/c9-16395087[3]
Początek drogi do idealnego cementu – wydobycie i przygotowanie surowców naturalnych
Produkcja cementu to fascynujący proces, który rozpoczyna się od wydobycia podstawowych surowców. Kopaliny naturalne, takie jak wapień, margiel i glina, stanowią fundament tego niezwykłego materiału budowlanego. Wydobycie tych cennych minerałów odbywa się w kopalniach odkrywkowych, często zlokalizowanych w bliskim sąsiedztwie cementowni, co znacząco redukuje koszty transportu i minimalizuje wpływ na środowisko.
Czy zastanawialiście się kiedyś, jak wygląda pierwszy etap produkcji cementu? To prawdziwe inżynieryjne wyzwanie! Nowoczesne metody wydobywcze łączą w sobie precyzję i efektywność. Wykorzystuje się zaawansowane techniki, takie jak odwierty w skale i kontrolowane roboty strzałowe, które pozwalają na selektywne pozyskiwanie surowców o najwyższej jakości. Co ciekawe, dzięki zastosowaniu innowacyjnych technologii, wpływ tych działań na otaczające środowisko jest znikomy.
Przygotowanie surowców – klucz do sukcesu
Po wydobyciu, surowce przechodzą przez szereg procesów przygotowawczych, które są kluczowe dla uzyskania cementu o idealnych właściwościach. Kruszenie i wstępne uśrednianie to pierwsze kroki na drodze do uzyskania jednorodnej mieszanki. Wykorzystuje się do tego celu potężne kruszarki, które rozdrabniają ogromne bloki skalne do rozmiarów umożliwiających dalszą obróbkę.
Następnie, rozdrobniony materiał poddawany jest procesowi homogenizacji. To niezwykle istotny etap, podczas którego surowce są dokładnie mieszane w odpowiednich proporcjach. Czy wiecie, że nawet niewielkie odchylenia w składzie mieszanki mogą znacząco wpłynąć na końcową jakość cementu? Dlatego też nowoczesne cementownie wykorzystują zaawansowane systemy kontroli jakości, które nieustannie monitorują skład surowca na każdym etapie produkcji.
Sugerujemy lekturę:
Ładuję link…
Innowacje w przygotowaniu surowców
Współczesna technologia produkcji cementu nie ogranicza się jedynie do tradycyjnych metod. Coraz częściej stosuje się innowacyjne rozwiązania, które pozwalają na optymalizację procesu i redukcję jego wpływu na środowisko. Jednym z takich rozwiązań jest wykorzystanie surowców alternatywnych, które mogą częściowo zastąpić naturalne kopaliny.
Do najczęściej stosowanych dodatków należą:
- Popioły lotne z elektrowni
- Żużle wielkopiecowe
- Pyły z produkcji krzemionki
Zastosowanie tych materiałów nie tylko pozwala na bardziej zrównoważoną produkcję, ale także może wpłynąć na poprawę właściwości końcowego produktu. To fascynujące, jak przemysł cementowy ewoluuje, łącząc tradycję z nowoczesnością, prawda? Każdy etap produkcji, począwszy od wydobycia surowców, jest starannie przemyślany i zoptymalizowany, aby zapewnić najwyższą jakość cementu, który będzie służył nam przez długie lata w najróżniejszych konstrukcjach.
Wysokie temperatury i precyzja – proces wypalania klinkieru jako kluczowy etap produkcji cementu
Wypalanie klinkieru stanowi najbardziej energochłonny i technologicznie złożony etap produkcji cementu, podczas którego przemiały surowiec przechodzi fascynujące przemiany fizykochemiczne. Proces ten realizowany jest w specjalnych piecach obrotowych – pochylonych, obracających się walcach o średnicy kilku metrów i długości sięgającej kilkudziesięciu metrów. To właśnie w tych kolosalnych urządzeniach mąka surowcowa poddawana jest ekstremalnym temperaturom, które w strefie spiekania osiągają wartość około 1450°C. A czy wiesz, że temperatura płomienia i gazów może sięgać nawet 2000°C? W tych warunkach materiał przechodzi fascynującą transformację – ze stanu stałego w ciekły, aby następnie po spieczeniu powrócić do postaci stałej, ale już z zupełnie nowymi właściwościami. Surowiec w najgorętszej strefie pieca przebywa stosunkowo krótko, bo około 30 minut, ale ten czas w zupełności wystarcza do zajścia wszystkich niezbędnych reakcji chemicznych. Nowoczesne piece cementowe wyposażone są w rozbudowane systemy wymienników ciepła, które znacząco poprawiają efektywność energetyczną całego procesu. Warto zaznaczyć, że niektóre zaawansowane instalacje posiadają również kalcynatory, umożliwiające spalanie części paliwa poza głównym walczakiem pieca.
Podczas procesu wypalania zachodzą niezwykle istotne reakcje chemiczne, w wyniku których powstają charakterystyczne minerały klinkierowe nadające cementowi jego wyjątkowe właściwości wiążące. Do najważniejszych faz mineralnych klinkieru zaliczamy krzemian trójwapniowy (alit), krzemian dwuwapniowy (belit), glinian trójwapniowy (celit) oraz glinożelazian czterowapniowy (braunmilleryt). Proporcje tych składników muszą być ściśle kontrolowane, ponieważ bezpośrednio wpływają na jakość końcowego produktu. Ciekawostką jest fakt, że popiół powstający ze spalania paliwa nie stanowi odpadu, lecz miesza się z wypalanym materiałem i staje się integralną częścią klinkieru. Taka bezodpadowość procesu to jeden z jego największych atutów z perspektywy ekologicznej. Warto również wspomnieć o alkalicznym charakterze materiału w piecu (z dominującym tlenkiem wapnia), który neutralizuje kwaśne składniki gazów odlotowych, co stanowi kolejną ekologiczną zaletę procesu.
Kontrola i precyzja w sercu procesu wypalania
Precyzyjna kontrola warunków termicznych wewnątrz pieca obrotowego to absolutna podstawa udanego procesu produkcji klinkieru. Współczesne cementownie wykorzystują zaawansowane systemy monitorowania i sterowania, które pozwalają na ciągłą obserwację i regulację kluczowych parametrów. Zbyt niska temperatura może skutkować niepełnym przereagowaniem składników, podczas gdy zbyt wysoka prowadzi do nadmiernego zużycia wymurówki pieca i zwiększonej emisji zanieczyszczeń. Dlatego piece wyposażone są w rozlokowane strategicznie czujniki temperatury, analizatory składu gazów oraz systemy wizualizacji procesu. W zasadzie można powiedzieć, że serce nowoczesnej cementowni bije w rytm danych płynących z tych zaawansowanych systemów monitoringu. Ważnym aspektem jest dystrybucja ciepła wzdłuż pieca, która powinna zapewniać stopniowe podgrzewanie materiału w miarę jego wędrówki w kierunku strefy spiekania. Z technologicznego punktu widzenia, stabilność pracy pieca jest kluczowa – każde zakłócenie równowagi termicznej może zaburzyć delikatną choreografię reakcji chemicznych i negatywnie wpłynąć na jakość produkowanego klinkieru. Inżynierowie cementowni doskonale wiedzą, że utrzymanie optymalnych parametrów procesu wymaga nie tylko wiedzy i doświadczenia, ale również ciągłej czujności i gotowości do natychmiastowej reakcji na wszelkie odchylenia od normy.
Przemieszczanie materiału przez piec jest równie fascynującym aspektem całego procesu. Pochylenie i obrót walczaka powodują stopniowe przesuwanie się surowca od wyższego końca do niższego, gdzie znajduje się palnik. Prędkość rotacji pieca bezpośrednio wpływa na tempo wędrówki materiału i czas jego przebywania w poszczególnych strefach termicznych. Wewnętrzna powierzchnia pieca wyłożona jest specjalną wymurówką wykonaną z materiałów ogniotrwałych, zdolnych do pracy w ekstremalnie wysokich temperaturach przez długi czas. Ta wymurówka stanowi nie tylko barierę ochronną dla stalowego płaszcza pieca, ale również pełni funkcję akumulatora ciepła, zapewniając większą stabilność termiczną całego procesu.
Chemiczna symfonia wysokich temperatur
Proces wypalania klinkieru to prawdziwy koncert reakcji chemicznych, które następują po sobie w ściśle określonej kolejności. Wszystko rozpoczyna się od:
- Odparowania wody w temperaturze około 100-200°C
- Dekarbonatyzacji (rozkładu węglanu wapnia) w zakresie 500-900°C
- Powstawania pierwszych faz ciekłych powyżej 900°C
- Tworzenia minerałów klinkierowych w najwyższych temperaturach
- Krystalizacji i stabilizacji struktury w fazie chłodzenia
Najważniejszym momentem jest tworzenie się alitu (krzemianu trójwapniowego), który odpowiada za szybkie narastanie wytrzymałości cementu we wczesnym okresie po związaniu. Cały ten proces można porównać do skomplikowanej choreografii, w której każdy ruch musi nastąpić dokładnie we właściwym momencie. Warto zauważyć, że skład mineralny klinkieru można modyfikować poprzez odpowiedni dobór surowców oraz parametrów procesu wypalania, co pozwala na produkcję różnych rodzajów cementu o zróżnicowanych właściwościach technicznych. W procesie wypalania istotną rolę odgrywają również tzw. mineralizatory – substancje, które nawet w niewielkich ilościach mogą znacząco wpływać na przebieg reakcji chemicznych. Mogą one obniżać temperaturę powstawania fazy ciekłej, przyspieszać reakcje tworzenia minerałów klinkierowych lub modyfikować ich właściwości. To fascynujące, jak niewielkie ilości tych substancji mogą dramatycznie zmienić przebieg całego procesu i właściwości końcowego produktu. Z pewnością można powiedzieć, że mimo iż technologia produkcji cementu ma już ponad 150 lat, to wciąż kryje ona wiele tajemnic i możliwości udoskonaleń, nad którymi nieustannie pracują inżynierowie i naukowcy.
Po zakończeniu procesu wypalania, gorący klinkier (o temperaturze około 900-1300°C) jest kierowany do chłodnika, gdzie jego temperatura zostaje szybko obniżona do około 100°C. Ten etap ma kluczowe znaczenie dla właściwości końcowego produktu, ponieważ szybkość chłodzenia wpływa na strukturę krystaliczną minerałów klinkierowych. Ciepło odebrane od klinkieru nie jest marnowane – nowoczesne instalacje odzyskują je i wykorzystują do podgrzewania powietrza używanego w procesie spalania, co dodatkowo poprawia efektywność energetyczną całego procesu.
Sztuka mieszania i mielenia – jak powstaje cement o różnych parametrach i klasach wytrzymałości
Proces mieszania i mielenia to fascynujący etap produkcji cementu, który w decydującym stopniu wpływa na ostateczne parametry i właściwości tego kluczowego materiału budowlanego. Technolodzy cementowi z niemal zegarmistrzowską precyzją kontrolują ten proces, dostosowując każdy parametr do określonych wymagań rynkowych. Możesz się zastanawiać, dlaczego jeden cement szybciej wiąże, a inny ma większą odporność na agresywne środowisko? Odpowiedź kryje się właśnie w sztuce mieszania i mielenia. Dzięki nowoczesnym technologiom możliwe jest uzyskanie cementy o zróżnicowanych parametrach użytkowych. Wytrzymałość na ściskanie, czas wiązania czy odporność na czynniki chemiczne – wszystkie te cechy determinowane są na etapie mieszania i mielenia. Cement może być wykorzystywany zarówno do budowy domów jednorodzinnych, jak i do wznoszenia monumentalnych konstrukcji inżynieryjnych, a jego właściwości muszą być idealnie dobrane do konkretnego zastosowania.
W nowoczesnych cementowniach stosuje się różnorodne technologie mieszania i mielenia. Najczęściej wykorzystywane są młyny kulowe, w których rozdrobnienie następuje poprzez zderzenia stalowych kul z mielonym materiałem. Innym rozwiązaniem są młyny pionowe, gdzie materiał jest miażdżony przez stożkowe rolki dociskające go do obracającego się stołu. Stopień rozdrobnienia cząstek cementu ma kluczowy wpływ na jego reaktywność i czas wiązania. Zbyt grube cząstki nie hydratyzują w pełni, co oznacza niepełne wykorzystanie potencjału wiążącego. Z kolei zbyt drobny przemiał może prowadzić do problemów logistycznych i nadmiernego zużycia energii. To prawdziwa sztuka znaleźć złoty środek! Precyzyjne przygotowanie i homogenizacja surowców stanowią fundament wysokiej jakości produktu końcowego. Dlatego nowoczesne cementownie wyposażone są w zaawansowane systemy kontroli składu chemicznego i fizycznych właściwości mieszanki na każdym etapie procesu.
Dodatki modyfikujące właściwości – klucz do różnorodności cementów
Na etapie przemiału klinkieru wprowadza się dodatki, które radykalnie zmieniają właściwości gotowego cementu. Najważniejszym dodatkiem jest gips (siarczan wapnia), który pełni rolę regulatora czasu wiązania. Bez gipsu cement wiązałby tak szybko, że praktycznie niemożliwe byłoby jego zastosowanie na budowie. W procesie mielenia stosuje się również szereg innych dodatków, które nadają cementowi specyficzne właściwości:
- Żużel wielkopiecowy – poprawia odporność na agresywne środowiska chemiczne i zmniejsza ciepło hydratacji
- Popioły lotne – zwiększają urabialność mieszanek betonowych i poprawiają szczelność betonu
- Wapień – pozwala na redukcję emisji CO2 i poprawia urabialność cementu
- Pucolany naturalne – zwiększają odporność na korozję chemiczną
Proporcje tych dodatków są ściśle kontrolowane i dostosowywane do wymagań dotyczących konkretnego typu cementu. Europejskie normy definiują kilka głównych typów cementów (CEM I do CEM V), które różnią się rodzajem i ilością dodatków, co przekłada się na ich właściwości techniczne. Fascynujące, jak niewielka zmiana proporcji dodatków może całkowicie zmienić charakterystykę materiału! Warto podkreślić, że dodatki mają również istotny wymiar ekologiczny – wykorzystanie materiałów odpadowych, takich jak popioły lotne czy żużle hutnicze, pozwala zagospodarować produkty uboczne innych gałęzi przemysłu, jednocześnie redukując ślad węglowy cementu.
Klasy wytrzymałości a proces mielenia
Klasy wytrzymałości cementu, oznaczane symbolami 32,5, 42,5 czy 52,5, są bezpośrednio związane z procesem mielenia. Wartości te określają minimalną wytrzymałość na ściskanie po 28 dniach (wyrażoną w MPa). Drobniejszy przemiał zwiększa powierzchnię kontaktu cząstek cementu z wodą, co przyspiesza proces hydratacji i prowadzi do uzyskania wyższej wytrzymałości. Jednocześnie jednak zwiększa energochłonność procesu produkcyjnego. Nowoczesne młyny cementowe wyposażone są w zaawansowane systemy separacji, które pozwalają na precyzyjne rozdzielenie frakcji o różnej wielkości. Materiał niedostatecznie zmielony kierowany jest z powrotem do młyna, co zapewnia jednorodność produktu końcowego. To niesamowite, jak precyzyjnie możemy kontrolować ten proces! Zaawansowane systemy kontroli w czasie rzeczywistym monitorują kluczowe parametry, takie jak granulacja cząstek czy temperatura procesu, gwarantując utrzymanie właściwości cementu w ściśle określonych granicach. Optymalizacja procesu mieszania i mielenia pozwala również na redukcję zużycia energii, co przekłada się na mniejszą emisję CO2 i innych gazów cieplarnianych. W ten sposób przemysł cementowy dąży do ograniczenia swojego wpływu na środowisko, jednocześnie utrzymując wysoką jakość produktów.
Jakość i kontrola w produkcji cementu – gwarancja idealnego materiału budowlanego
Produkcja cementu wysokiej jakości wymaga rygorystycznych systemów kontroli na każdym etapie procesu. Od wydobycia surowców, przez ich przygotowanie, wypalanie klinkieru, aż po mielenie i pakowanie gotowego produktu, każdy krok podlega szczegółowym procedurom kontrolnym. W nowoczesnych cementowniach stosuje się zaawansowane technologicznie systemy monitorowania, które w czasie rzeczywistym śledzą parametry produkcji. Czy zastanawiałeś się kiedyś, ile punktów kontrolnych musi przejść cement zanim trafi na plac budowy? W rzeczywistości są ich dziesiątki!
Kluczowy z punktu widzenia jakości jest proces wypalania klinkieru, gdzie precyzyjne utrzymanie profilu temperaturowego w piecu obrotowym determinuje właściwości mineralogiczne materiału. Zaawansowane systemy sterowania, często oparte na algorytmach sztucznej inteligencji, pozwalają na utrzymanie idealnych warunków reakcji.
Nowoczesne metody testowania jakości
W laboratoriach cementowni prowadzi się szereg testów weryfikujących zgodność cementu z normami:
- Testy wytrzymałości na ściskanie
- Pomiary czasu wiązania
- Badania stałości objętości
- Analiza miałkości cząstek
- Badania składu chemicznego
Technologie machine learning pozwalają na przewidywanie potencjalnych problemów jakościowych zanim jeszcze się pojawią. Kontrola jakości ewoluuje od podejścia reaktywnego do predykcyjnego, podnosząc efektywność produkcji.
Trwałość konstrukcji jako efekt wysokiej jakości
Rygorystyczna kontrola jakości cementu przekłada się bezpośrednio na trwałość konstrukcji budowlanych. Cement jest składnikiem betonu – materiału, który musi wytrzymać dziesiątki lat eksploatacji w zróżnicowanych warunkach. Czy zdajesz sobie sprawę, że jakość cementu może zadecydować o trwałości mostu przez kolejne sto lat?
W przypadku obiektów o wysokich wymaganiach, takich jak elektrownie czy tamy, parametry cementu podlegają dodatkowym, zaostrzonym kryteriom. Dla takich zastosowań często opracowuje się specjalne odmiany cementu o precyzyjnie kontrolowanych właściwościach.
Podsumowanie
Produkcja cementu to fascynujący proces technologiczny łączący tradycyjne metody z nowoczesnymi technologiami. Rygorystyczne systemy kontroli jakości gwarantują, że cement spełnia najwyższe wymagania. Dzięki temu możliwe jest wznoszenie trwałych i bezpiecznych konstrukcji budowlanych, które służą społeczeństwu przez długie lata. Cement pozostaje jednym z najważniejszych materiałów konstrukcyjnych, bez którego trudno wyobrazić sobie współczesne budownictwo.
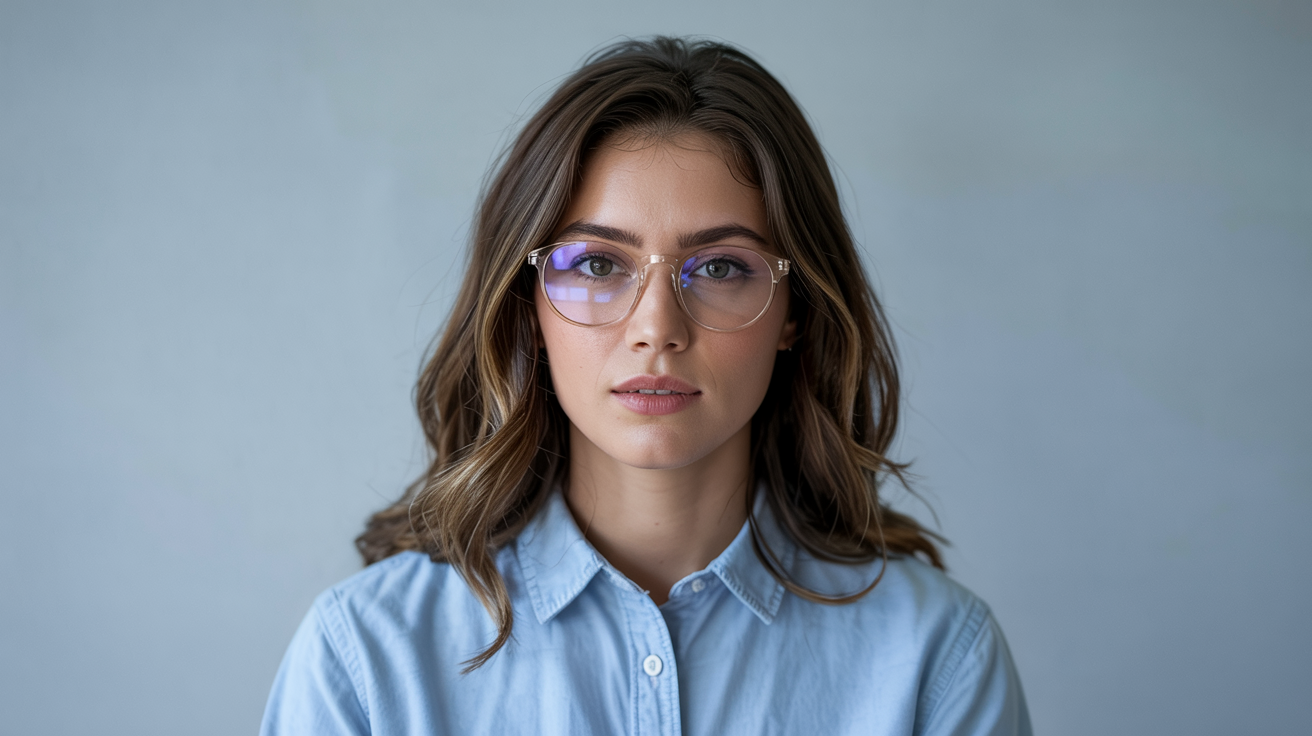
Nazywam się Justyna Lewicka, budownictwo, remonty i dekoracja wnętrz to nie tylko moja praca – to sposób na życie. Na lewickajustyna.pl znajdziesz miejsce, gdzie dzielę się swoją wiedzą, doświadczeniem oraz niegasnącą pasją do tworzenia pięknych i funkcjonalnych przestrzeni. Zapraszam do lektury i do wspólnego odkrywania nieskończonych możliwości, jakie daje majsterkowanie. [email protected]